
Онлайн книга «Производственная система Тойоты: уходя от массового производства»
Обычно в бизнесе ответы на вопросы что, когда и сколько разрабатываются в плановом отделе и выпускаются в виде плана начала работ, плана перевозок, заказа на производство или заказа на доставку, которые распространяются внутри предприятия.
При использовании такой системы ответ на вопрос когда формулируется приблизительно, и никого не волнует, если детали поступят раньше. Однако для регулирования распределения деталей, которые произведены слишком рано, приходится задействовать много лишних рабочих. Слово «точно» в термине «точно вовремя» об этом и говорит. Если комплектующие поступают раньше нужного времени — не в точно определенный срок, потерь избежать не удастся.
В производственной системе Тойоты благодаря канбану удается полностью избежать перепроизводства. В результате не возникает лишних запасов, а следовательно, нет необходимости в складских помещениях и работниках склада. Кроме того, отпадает потребность в кипах ненужных документов.
Неправильное применение порождает проблемы
С хорошим инструментом можно добиться замечательных результатов. Канбан относится к тем инструментам, которые при неверном использовании могут создать массу проблем.
Чтобы правильно и грамотно использовать канбан, мы постарались четко сформулировать для себя цель его применения и роль, а затем установить правила использования.
Канбан позволяет добиться поставки точно вовремя, поскольку его цель состоит именно в своевременности поставки. В сущности, канбан становится автономным нервом производственной линии. С его помощью рабочие начинают функционировать самостоятельно и сами решают, необходима ли сверхурочная работа. Система «канбан» также выявляет, что еще должны сделать менеджеры и супервайзеры для улучшения производства. Это, вне всякого сомнения, способствует повышению производительности труда и работы оборудования.
Канбан также обращает внимание на необходимость исключения потерь. Его применение стимулирует творческое мышление и инициативу, и сразу же становится ясно, где существуют потери. На заводе канбан является мощным фактором, способствующим сокращению лишней рабочей силы и запасов, исключению производства дефектной продукции и предотвращению выхода из строя оборудования.
Можно без преувеличения сказать, что канбан управляет потоком продукции и всем производственным процессом компании Toyota с оборотом более 4,8 миллиарда долларов в год.
Таким образом, система «канбан» отвечает потребностям нашей компании. Она функционирует с соблюдением строгих правил, и ее результативность доказана успехами компании.
Вместе с тем производственная система Тойоты постоянно развивается и изменяется, поэтому строгое соблюдение правил работы с канбаном является жизненно важным.
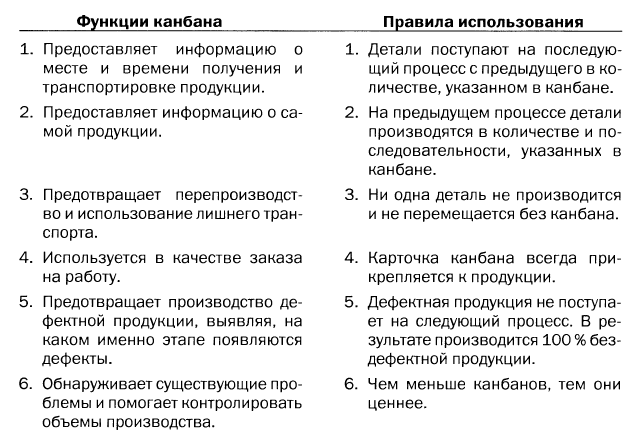
Чтобы переосмыслить то, что называется здравым смыслом, нужны талант и смелость
Согласно первому правилу канбана детали поступают на последующий процесс с предыдущего в количестве, указанном в канбане. Это правило было выведено из необходимости взгляда на вещи в перевернутом виде, с противоположной стороны.
Для использования этого правила недостаточно поверхностного понимания вопроса. Высшее руководство должно изменить свой образ мышления и решиться повернуть вспять традиционный поток производства, транспортировки и поставки. Для этого потребуется смелость, поскольку возникнет мощное сопротивление. Однако чем больше упорства, тем успешнее станет внедрение производственной системы Тойоты.
Все 30 лет работы в автомобильной промышленности я постоянно занимался продвижением производственной системы
Тойоты, хотя и не всегда был уверен в успехе.
Может быть, это прозвучит слишком самонадеянно, но распространение производственной системы Тойоты совпадало с моим продвижением по служебной лестнице в компании.
В 1949-1950 гг., будучи управляющим механического цеха, который теперь стал головным производственным предприятием, я сделал первые шаги к воплощению идеи «точно вовремя». Затем для создания производственного потока мы переставили станки и применили многостаночный метод, при котором один работник управляет тремя или четырьмя станками, имеющими различные функции. С тех пор я максимально использовал свой растущий авторитет для того, чтобы распространять эти идеи.
Все идеи, которые я так смело применял на практике, были нацелены на улучшение старой, консервативной производственной системы — и, возможно, мои действия иногда казались слишком своевольными. Высшее руководство компании Toyota наблюдало за ситуацией спокойно, и я восхищаюсь занятой им позицией.
У меня есть серьезная причина подчеркивать роль высшего руководства в обсуждении первого правила канбана. Дело в том, что на пути внедрения правила, согласно которому последующий процесс должен брать от предыдущего детали в необходимом количестве и в нужное время, возникает много препятствий. По этой причине согласие и мощная поддержка со стороны руководства необходимы для успешного применения первого правила.
Для предыдущего процесса это означает исключение производственного графика, которого так долго придерживались. Рабочим психологически трудно принять и свыкнуться с мыслью, что простое производство как можно большего количества деталей перестало быть их главной задачей.
Стремление производить лишь то количество изделий, которое требуется последующему процессу, означает более частое выполнение переналадки оборудования, если только линия не рассчитана на изготовление единичной номенклатуры деталей.
Обычно считается преимуществом выпускать на предыдущем производственном процессе крупные партии одинаковых изделий. Но производить изделия А и Б одновременно и в требуемом количестве во время одного процесса невозможно. Следовательно, встает необходимость сокращать время переналадки оборудования и уменьшать размер партий производимых изделий.
Среди новых проблем самой сложной является та, которая возникает при необходимости поставки на последующий процесс большого объема однотипных деталей. В этом случае на предыдущем процессе сразу же обнаруживаются ограничения технологических возможностей производства. Можно попробовать решить эту проблему, создав определенный запас изделий, однако мы не знаем точно, какое изделие понадобится в следующий период, и тогда нам придется создавать запасы для каждого вида изделий: А, Б и т.д. Если мы будем делать так на каждом участке, то в каждом углу завода будут грудами храниться узлы и детали.
Следовательно, для того чтобы внедрить систему, при которой последующий процесс забирает нужные детали, необходимо будет изменить методы производства как на последующем, так и на предыдущем процессах.
Шаг за шагом я все же пришел к решению проблемы, связанной с приведенной выше ситуацией. Учебников у нас не было, поэтому выяснить, какими будут результаты наших действий, мы могли лишь опытным путем. По мере того, как мы делали попытки, вносили корректировки, делали новые попытки и вновь корректировали свои действия, напряжение все нарастало. Путём таких проб и ошибок я внедрил систему запроса изделий с последующих процессов внутри всей компании. Эксперименты всегда проводились на заводе, который не получал деталей от внешних поставщиков, поскольку мы решили отладить новую систему сначала внутри самой компании.